Menu
HOME / R&D / Inventing technology / DLC

DLC
DLC (Diamond-Like Carbon)
- Carbon (atomic symbol: C) is an important element to divide organic and inorganic substances. Carbon exhibits completely different physical properties depending on its bonds. If it has only sp3 bonds, it forms diamond, and if it has only sp2 bonds, it forms graphite.
- DLC coating is a plasma surface treatment technology that deposit thin film by electrically accelerating carbon ions or activated hydrocarbon molecules in plasma to collide onto a substrate. Unlike diamonds and graphite, DLC is amorphous thin film with a mixture of sp, sp2, and sp3 bonds.
- DLC has excellent physical properties such as hardness, corrosion resistance, abrasion resistance, and coefficient of friction that are comparable to diamond, so the name Diamond-Like Carbon (DLC) is widely used.

Diamond Structure (sp3)
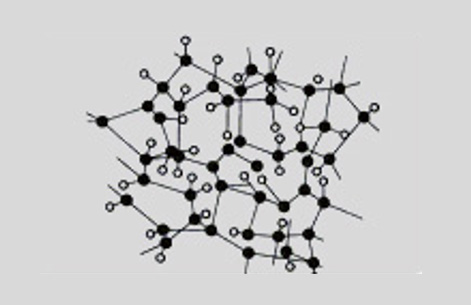
Amorphous Structure (sp2, sp3)
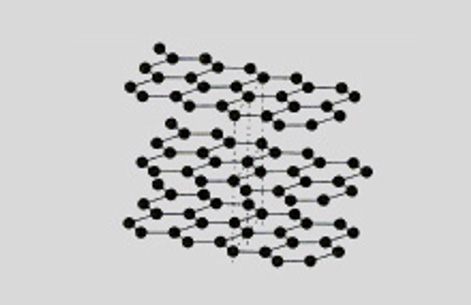
Graphite Structure (sp2)
Physical Properties Comparison : DLC / Diamond / Graphite
Properties | Diamond | DLC | Graphite |
Density (g/cm3) | 3.51 | 1.8 – 3.6 | 2.26 |
Hardness (Kgf/mm2) | 10000 | 2000 – 8000 | 500 |
Friction coefficient | 0.05 | 0.03 – 0.2 | 0.1 |
Refractive index | 2.42 | 1.8 – 2.6 | 2.15 – 1.8 |
Light transmit | UV-VIS-IR | VIS-IR | Opaque |
Resistance (Wcm) | > 1016 | 1010 – 1013 | 0.2 – 0.4 |
Structure of DLC coating
- DLC containing hydrogen is called a-C:H (Hydrogenated Amorphous Carbon).
- Amorphous carbon thin film without hydrogen is called ta-C (Tetrahedral Amorphous Carbon).
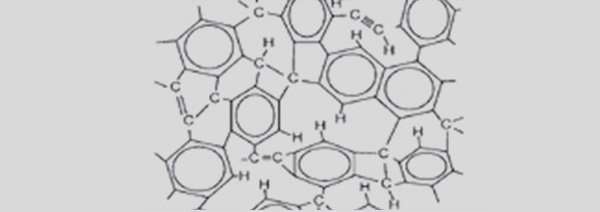
a-C:H Structure
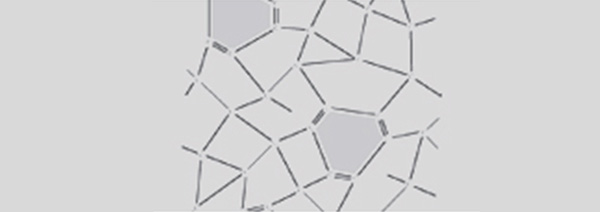
ta-C Structure
Multi-Layer DLC Coating
- DLC’s high residual stress occurred in its synthesis weaken the adhesion of thin film and it lowers the durability of the coated products. For DLC coated products, thin film peeling off due to low adhesion is more often the cause of shortened lifespan than the thin film itself is damaged such as abrasion. Therefore the adhesion is as important as the physical properties of the thin film itself.
- For improving the adhesion of DLC, we have developed various types of buffer layers. By depositing of a buffer layer suitable for metal or non-metal materials such as carbide, carbon steel, aluminum, brass, glass and plastic, we improved the bonding strength of DLC dramatically.
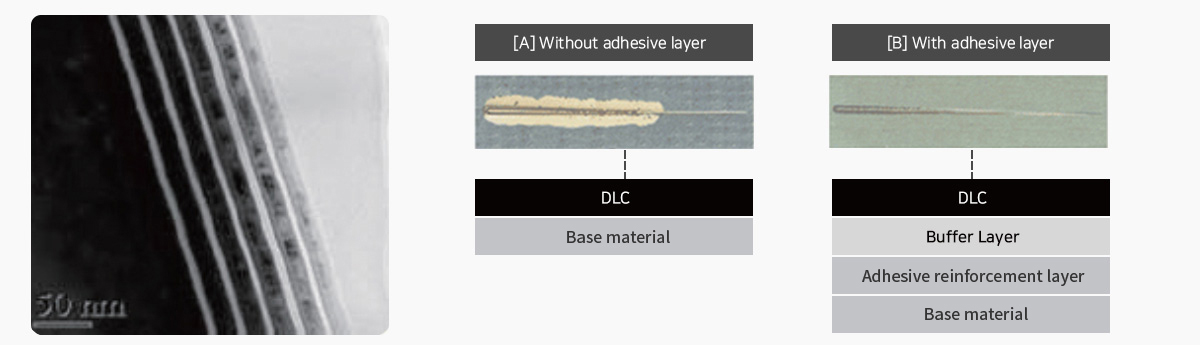